Many people forecast that the next months ahead is the economy’s best chance to gradually recover from the adverse effects of the global pandemic. While current U.S. inflation rates and the fear of another spike would say otherwise, increasing economic activity from business startups is proving a net positive turnout. Furthermore, the rise of the gig economy and a boom in a self-starter mindset toward 2022 are making waves for small businesses to grow and expand, making up for the opportunity costs of years prior.
However, while recent events in the business landscape and many industries show signs of recovery, one glaring issue that many newbie entrepreneurs and aspiring business owners fail to understand is their strict liability for their manufactured goods and products. And while rapid growth, proficient marketing, and aggressive sales tactics may appear more urgent on paper, failure to exercise due care will create cascading legal problems in the form of lawsuits suing for negligence and compensatory damages. While building an in-house legal team and knowing when your papers are served are beneficial, understanding the basics and intricacies of product liability is imperative.
What Is Product Liability, and How Does It Affect Businesses?
Companies, firms, and any organization in the business of manufacturing, selling, or leasing goods to consumers can be held liable for any physical harm or damage caused by said goods to the end-users. This concept is known as product liability. Because the law recognizes the necessity of protecting everyone’s physical safety, this liability offers remedies for people to seek compensation for any damage suffered.
In a nutshell, it serves the purpose of holding businesses accountable for their actions, protecting consumer safety, and directly encouraging companies to implement the necessary preventive and detective control activities to reduce the risk of injury. In addition, privity of contract doesn’t apply in this context; therefore, users who didn’t purchase the product themselves can still sue if they sustain injury caused by any defects of a faulty item. That being the case, failure to observe this level of professionalism and social responsibility can ruin the brand image and lead to expensive legal costs.
Practice Due Care in Specific Areas of Manufacturing
Given the risks associated with negligence, any business startup with plans to expand and grow its operations beyond small transactions must practice due care as early as possible in specific areas of manufacturing their goods to reasonably assure the customer’s safety. Specifically, the key processes to watch out for include designing and testing the product, improving the supplier selection process, adding appropriate warning labels on finished goods, and establishing a final inspection.
Designing the Product and Testing Its Prototype
Product design is the first and most crucial step in the process of creating merchandise and goods that consumers need, but apart from following trends in emerging demand, you must also test for possible risks. As a result, substantive measures in testing prototypes and ethical sampling methods are essential during the early stages of production. Any amount invested in this step will promise returns twofold much later.
Selection of Suppliers and Acquisition of Materials
In today’s market, recovery for the global supply chain is bleak, but even with inventories operating at substandard just-in-time management systems, the acquisition of quality materials is important. Your finished product is only as good as the raw materials utilized, and partnering with suppliers who can’t 100% guarantee industry standard condition and safety will implicate you in legal issues. So, evaluate their bid submission and review their quality assurance programs.
Addition of Proper Warning Labels and Stickers
A company can create a near-perfect product on paper with zero defects when shipped but still end up facing product liability lawsuits for inadequate instructions and the lack of warning labels. As a result, manufacturers and distributors must warn users as best possible and highlight the correct method of implementing the goods according to guidelines. Nevertheless, these warnings are never bulletproof, but if we can steer usage as intended, it can significantly reduce the risks of legal action.
Final Inspection Before Shipping Out to Customers
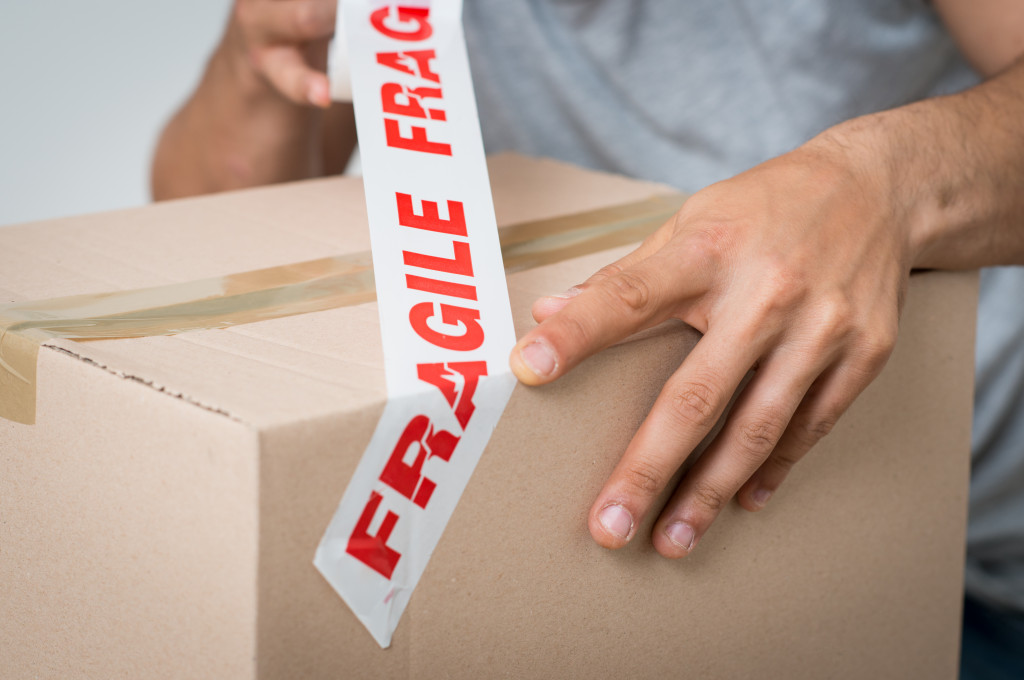
No production or assembly line is without the risk of errors. Unless you’re fully automated with robotics that guarantees 100% uptime, implementing a final inspection before the shipping process is an excellent method of correcting any undetected issues. At the end of the day, we can never reach absolute assurance of no problems encountered. Still, any procedure that can increase consumer confidence must be observed as much as possible.
Lawsuits Are Unavoidable, but They Shouldn’t Cripple Your Business
Lawsuits come with the territory of business, and apart from hiring a skilled legal department, understanding the ins and outs of product liability is non-negotiable for aspiring entrepreneurs. So, before you invest in product development, you must allocate resources to quality assurance and control procedures first.